Fasteners and Machining: Maximizing Style for Superior Production
Browsing the World of Fasteners and Machining: Techniques for Precision and Rate
In the detailed realm of bolts and machining, the pursuit for accuracy and rate is a perpetual challenge that requires thorough focus to detail and tactical planning. From recognizing the diverse variety of fastener types to choosing optimal materials that can stand up to rigorous demands, each action in the procedure plays an essential function in attaining the preferred result. Accuracy machining methods further raise the complexity of this craft, needing a delicate balance in between technological expertise and ingenious techniques. As we delve right into the techniques that can improve both rate and efficiency in this domain, the interplay between quality assurance actions and operational excellence becomes an important focal factor.
Understanding Fastener Types
When choosing fasteners for a project, understanding the numerous kinds offered is vital for making certain optimum efficiency and dependability. Fasteners come in a vast array of kinds, each developed for particular applications and requirements. Bolts are utilized with nuts to hold materials with each other, while screws are functional fasteners that can be used with or without a nut, relying on the application. Nuts, on the other hand, are internally threaded bolts that friend with screws or bolts, giving a safe hold. Washers are important for dispersing the tons of the fastener and protecting against damage to the material being attached. Furthermore, rivets are permanent bolts that are optimal for applications where disassembly is not needed. Understanding the distinctions between these fastener kinds is vital for picking the right one for the task, ensuring that the link is strong, resilient, and dependable. By picking the appropriate bolt type, you can enhance the efficiency and longevity of your task - Fasteners and Machining.
Selecting the Right Materials
Recognizing the importance of selecting the ideal products is paramount in guaranteeing the optimum efficiency and reliability of the chosen fastener types reviewed previously. When it concerns bolts and machining applications, the product option plays an essential function in figuring out the total toughness, durability, rust resistance, and compatibility with the designated atmosphere. Different products use differing residential properties that can significantly affect the efficiency of the fasteners.
Typical products utilized for fasteners include steel, stainless steel, aluminum, titanium, and brass, each having its one-of-a-kind toughness and weak points. Steel is renowned for its high stamina and longevity, making it ideal for a vast array of applications. Stainless-steel uses exceptional rust resistance, ideal for environments vulnerable to moisture and chemicals. Light weight aluminum is corrosion-resistant and lightweight, making it suitable for applications where weight reduction is critical. Brass is usually selected for its aesthetic appeal and superb conductivity. Titanium is understood for its outstanding strength-to-weight ratio, making it optimal for high-performance applications. Selecting the appropriate product includes considering aspects such as strength needs, ecological conditions, and spending plan restrictions to ensure the wanted performance and longevity of the bolts.
Accuracy Machining Techniques

In addition to CNC machining, various other precision strategies like grinding, turning, milling, and boring play vital functions in bolt production. Grinding assists attain fine surface area finishes and tight dimensional resistances, while transforming is typically made use of to create cylindrical parts with precise sizes. Milling and drilling operations are crucial for shaping and producing openings in bolts, ensuring they meet precise specifications and function properly.
Enhancing Rate and Efficiency
To optimize fastener manufacturing procedures, it is important to improve procedures and execute reliable approaches that complement precision machining methods. One crucial method for boosting rate and performance is the application of lean production concepts. By lowering waste and focusing on continuous improvement, lean practices help get rid of bottlenecks and enhance process. Furthermore, buying automation innovations can dramatically enhance manufacturing rate. Automated systems can deal with repeated tasks with precision and speed, allowing workers to focus on more complex and value-added activities. Taking On Just-In-Time (JIT) stock management can also enhance performance by making certain that the appropriate products are offered at the ideal time, lessening excess stock and decreasing lead look these up times. Furthermore, cultivating a society of collaboration and communication amongst group members can enhance total effectiveness by promoting openness, analytical, and innovation. By incorporating these approaches, makers can attain a balance between rate and accuracy, inevitably enhancing their one-upmanship in the bolt market.
Quality Assurance Procedures
Implementing strenuous top quality control procedures is essential in making certain the integrity and uniformity of bolt items in the production process. Quality assurance procedures include different phases, beginning with the selection of basic materials to the final assessment of the completed bolts. One fundamental element of quality assurance is performing comprehensive material examinations to verify compliance with specifications. This entails analyzing variables such as product make-up, stamina, and toughness to guarantee that the fasteners meet industry standards. Additionally, keeping an eye on the machining refines is important to maintain dimensional accuracy and surface coating top quality. Making use of innovative modern technology, such as automatic evaluation systems and precision measuring devices, can improve the accuracy and efficiency of top quality control treatments.
Normal calibration of equipment and machinery is important to keep consistency in production and make certain that fasteners satisfy the needed tolerances. Executing stringent protocols for identifying and resolving non-conformities or issues is crucial in preventing substandard items from entering the market. By developing a thorough quality control framework, makers can promote the reputation of their brand and provide fasteners that fulfill the highest standards of performance and toughness.
Verdict
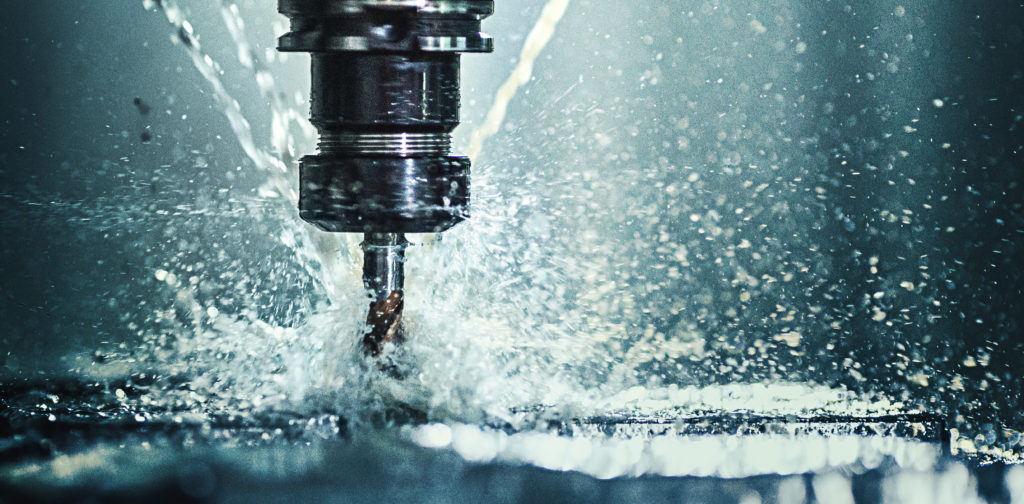
In the complex world of bolts and machining, the mission for precision and rate is a perpetual challenge that requires thorough focus to information and critical preparation. When it comes to bolts and machining applications, the material choice plays an important role in identifying the overall strength, resilience, corrosion resistance, and compatibility with the desired setting. Accuracy machining includes various advanced approaches that make sure the limited tolerances and requirements needed for fasteners.In addition to CNC machining, other precision techniques like grinding, transforming, milling, and boring play crucial functions in fastener manufacturing.To enhance fastener manufacturing procedures, it is vital to improve procedures and carry out efficient approaches that match precision machining strategies.